In 1965, the U.S.-built hydrofoil “Plainview (AGEH-1)” became a classic example of early adoption of 5456 aluminum alloy. Apart from its hydrofoil system, the vessel featured a fully welded aluminum structure using a total of 113.5 tons of aluminum materials. Notably, 80% of that comprised large extrusions made from 5456-H311 alloy, and thick plates were made from 5456-H321. Owing to its excellent mechanical properties and corrosion resistance, 5456 marine-grade aluminum has become an ideal material for key structural components in hydrofoil vessels.
Introduction to 5456 Aluminum Alloy
5456 marine aluminum belongs to the aluminum-magnesium anti-corrosion series, with magnesium as the primary alloying element in the range of 4.7% to 5.5%. It features good strength, corrosion resistance, and weldability, making it widely used in marine engineering, shipbuilding, and lightweight structural applications requiring high strength.
Compared to similar alloys like 5083 and 5086, 5456 offers higher strength, although its stress corrosion resistance in certain welded conditions may be slightly lower.
In practical applications, 5456 is selected as a hull material mainly due to its excellent welded joint strength. Typically:
Plates are used in temper states H116 and H117
Extrusions use the H111 temper, balancing formability and mechanical performance.
Specifications of 5456 Marine Aluminum Plate
Alloy | 5456 |
Temper | H116, H117, H311, H321, etc. |
Thickness | 3–50 mm |
Width | 1000–2650 mm |
Length | 1000–16000 mm |
Applications | Ideal for fast ferries, LNG spherical tank storage containers, hydrofoil boats, offshore workboats, and yachts. Commonly used in hull sides, bottom plates, portholes, structural containers, and side plates. |
Chemical Composition of 5456 Marine Aluminum (% by weight)
Alloy | Si | Fe | Cu | Mn | Mg | Cr | Zn | Ti | Ohter:Each | Other:Total | Al |
5456 | 0.40 | 0.40 | 0.10 | 0.4-1.0 | 4.0-4.9 | 0.05-0.25 | 0.25 | 0.15 | 0.05 | 0.15 | Remainder |
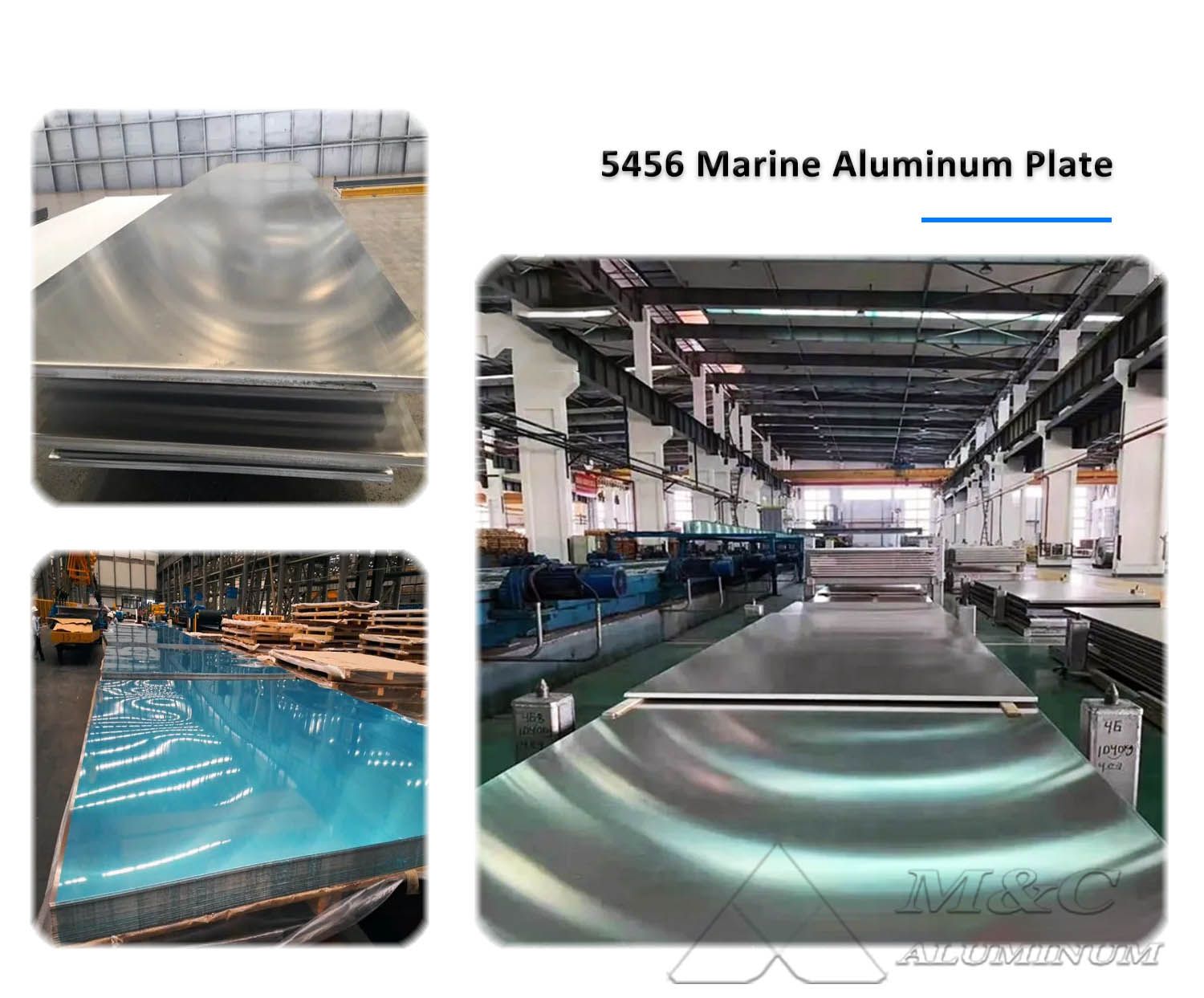
Key Features of 5456 Marine-Grade Aluminum Plate
1. Corrosion Resistance
As a member of the aluminum-magnesium anti-rust series, 5456 offers long-term resistance to seawater corrosion, minimizing rust risks in humid marine environments.
2. Lightweight Advantage
With a density about 1/3 that of steel, it significantly reduces vessel weight, improving hydrofoil speed and maneuverability.
3. Excellent Weldability and Workability
5456 aluminum surpasses steel in weldability, enabling complex hydrofoil structures and hull components to be built more efficiently and at a lower cost.
4. Vibration and Fatigue Resistance
Hydrofoils endure substantial hydrodynamic impact at high speeds. The toughness and vibration resistance of 5456 effectively reduce fatigue damage and extend service life.
5. Low-Temperature Performance
Even in cold marine environments, 5456 retains excellent mechanical properties, ensuring reliable vessel operation under harsh conditions.
Welding Techniques and Material Selection
To ensure structural integrity and welding quality in hydrofoil construction, 5356 aluminum welding wire, known for its superior crack resistance, is typically used. The following advanced welding methods are commonly applied:
Pulsed Metal Inert Gas (MIG) Welding
Spray Arc MIG Welding
Tungsten Inert Gas (TIG) Welding
These techniques help achieve strong welds while minimizing heat-affected zones, reducing residual stress and corrosion risks, and enhancing overall hull durability and reliability.
Specific Applications of 5456 Aluminum in Hydrofoil Boats
Hydrofoil Arms and Connecting Structures
The hydrofoil arms link the wings to the hull, bearing both lift and drag forces. These components demand high strength and fatigue resistance, making 5456 aluminum ideal for these load-bearing connections.Internal Reinforcements
Hull reinforcements such as stringers, longitudinal and transverse frames are essential for maintaining overall rigidity. 5456 aluminum is particularly suited for internal support structures not directly exposed to seawater.Power System Brackets and Bottom Framework
Areas like the engine room and propulsion system are subject to high vibration and thermal loads. 5456 aluminum provides structural stability and is highly adaptable to complex machining needs in these zones.
Comparison with Other Aluminum Alloys
In hydrofoil construction, alternatives like 5083, 6061, and 7075 are also used:
5083: Similar corrosion resistance and formability, but slightly lower strength than 5456.
6061: Offers good strength and weldability, but less corrosion-resistant in seawater compared to 5xxx series.
7075: Extremely high strength, but poor corrosion resistance—generally unsuitable for marine environments.
Overall, 5456 aluminum achieves a well-balanced combination of strength and corrosion resistance, making it an ideal material for marine structural applications like hydrofoils.